
Tuesday, November 6, 2007
Modular Construction: Evolution of the Construction Industry
Sunday, September 30, 2007
Construction Sector Grows Under 9MP
Organised by the Construction Industry Development Board (CIBD). ICW2007 was themed “Strengthening Construction Capabilities for Global Competitiveness”. “The Malaysian construction industry has contributed to the nation’s growth and it’s ready to venture overseas. The industry grew to 4.0 per cent during the first quarter under the Ninth Malaysia Plan and the formulation of a comprehensive Master Plan is timely to trigger a paradigm shift.
“However, there is a need to address issues and weaknesses before embarking on the vision of a progressive sector that thrives on knowledge, creativity for its survival.” CIBD chairman Tan Sri Jamilus Hussein said the event was a momentum and hallmark of the efforts to penetrate the challenging global market. “Malaysia has been transformed from a nation dependent on foreign experts and service providers to a major construction service exporter in the international market.
“Malaysian builders abroad have accumulated RM61 billion worth of projects covering about 38 countries. These projects are over a period of 10 years and currently our biggest overseas projects are in India and the Middle East. “We are also venturing into the Industrialised Building System (IBS) to reduce our dependency on foreign labour. IBS is not a new thing but merely a different trend. “IBS, which presents a cheaper cost in volume and time, takes work from the site to the factories but it will take some time for the industry to get used to the idea,” said Jamilus. He added that the future outlook for the industry was that it would be very busy over the next years.
At the event, Mohd Zin also opened the 24th Malaysian International Building Exposition (Malbex 2007) held in conjunction with ICW 2007. Organised by Reeds Exhibitions Sdn Bhd and co organised by CIBD, Malbex 2007 ran for four days. Reeds Exhibitions general manager Michelle Lim said last years, exhibitors made some RM86.5mil worth of sales and a further RM325 mil of sales was expected to be concluded this year.
“About 200 companies, comprising leading international manufacturers from 19 countries, including at least 51 first-time participants, took part in the expo. “It is recognised regionally as an outstanding industry-wide event for the building and construction sector, organised for the exchange of ideas, knowledge and technology.” She added that more than 14,000 trade visitors were expected at Malbex 2007, including architects, developers, interiors, designers, contractors, and top buyers. For details on Malbex 2007, visit http://www.malbex.com.my/
(Source: The Star, 29th September 2007)
Friday, August 24, 2007
Cheap homes price to stay
“We can’t do this ... If we allow an increase, the common man will not be able to own a house.
“Also, we do not want to do something which will create a lot of unhappiness (among people from the lower-income group),” he said after performing the ground-breaking ceremony for a Universiti Teknologi Mara campus in Kg Beting, near here.
Abdullah said developers should instead find ways to reduce their costs such as adopting new construction methods. “You can adopt the IBS (Industrialised Building System) method which can reduce your cost of doing business,” he said.
He was responding to a statement by Real Estate and Housing Developers Association deputy president Datuk Michael Yam that developers were unable to absorb the increase in prices of construction materials. The association had proposed that prices of low-cost houses and flats be increased from RM42,000 to RM60,000.
Abdullah said the IBS method was effective as developers would not have to rely heavily on skilled workers. He said if developers built houses quickly, they would also be able to service their bank loans faster.
“Pemudah has come up with recommendations that can help speed up business,” he said.
Pemudah is a public-private sector initiative which aims to simplify business operations in Malaysia by improving government services. Abdullah said it was unfair to allow an increase simply because government servants recently got a salary hike.
“They were unable to buy houses previously. If you increase the price, then the civil servants who recently got a pay increase will never be able to own a house,” he said.
(Source: The Star 24th August 2007)
Saturday, August 11, 2007
MIGHT Annual Report 2006 - Industrialised Building System
With the impact of globalization have run deep into many industries, more efficient methods have been introduced and implemented in order to survive the challenging market ahead. Every product have improved dramatically and been produced in a higher quality and at a lower cost but with the exception of houses and buildings. Whilst, other industries have been thriving in terms of technology application, only small improvement has been made in making building processes more efficient.
Houses of the future should be similar to products like cars or computers today. It is built mostly in a factory with parts that is easy to replace or maintain. The construction industry can be transform by following what other sectors are already doing; standardize and accessorize. This effort can be achieve by overhauling the industry through technology implementation such as Industrialised Building System or IBS. IBS based on Construction Industry Development Board of Malaysia (CIDB) is defined as “Construction technique in which components are manufactured in a factory, on or off site, positioned and assembled into a structure with minimal additional site works.”
In many parts of the world, IBS takes its forms in an initiative called open building concept. Open building is an approach to the design of buildings and said to be representing a new wave in architecture. Open building is defined as an innovative approach to design and construction that enhances the efficiency of the building process, while increasing the variety, flexibility and quality of the product [1].
Developed countries such as Japan, Netherlands and USA to name a few, have already started to develop concept that is called ‘Open Source Building’. The concept of the open source building is similar to what has happened in the ICT industry whereby through standardization of jointing parts such as USB ports, consumers can buy computer equipment such as mouse or scanner anywhere in the world. The equipment can then be easily installed by the users as the connection from the equipment to the computer has been internationally standardized.
Local Scenario
The Malaysian construction industry as envisaged in the Third Outline Perspective Plan (OPP3) 2001-2010, is expected to grow at 6.6% per annum during the period of OPP3 and contributes 3.1% to the GDP in the year 2010 [2]. The only way for the country to achieve this target is by increasing the industry’s efficiency and productivity to a higher level than it is now. In recognizing these critical factors, the Government has introduced a master plan to overhaul the construction industry into a more technology based industry. The master plan is called the “Industrialised Building Systems (IBS) Roadmap 2003-2010”. Endorsed by the Cabinet in October 2003, the plan’s ultimate objective is for the industry to achieve Open Building by the year 2010.
The IBS agenda was further boosted as the Government have announced in Budget 2005, whereby all new Government projects are required to have at least 50 per cent IBS content. This was subsequently followed by another announcement in Budget 2006 whereby IBS manufacturers would be given tax incentives through Accelerated Capital Allowance (ACA) for expenses occurred in the purchase of moulds used for production of precast concrete components. In the year 2006 also, an IBS Centre was established under CIDB that will act as a one stop agency for IBS implementation. These initiatives done by the Government have given the IBS agenda the momentum that was badly needed before. It has also put the construction industry into the right path of achieving higher efficiency and productivity by the year 2020.
Company’s activities
For the year 2006, the company has been actively promoting the use of IBS through partnership with various parties and Government agencies. Among the key activities are:
Project Implementation
IBS Modular is now actively implementing IBS product development through an IBS Technopreneur programme. The programme is in line with the Government aspiration of creating more IBS suppliers by 2010.
Human Capital Development
IBS Industrial Skills Enhancement Programme (INSEP)
The programme consists of 60 students that started on September 2006. The objective of the programme is to enhance the skill of the participants with the knowledge of IBS and therefore creating more job opportunities for them in the market place. The programme partner for this program is Housing Research Centre (HRC), UPM.
International and Business Programme
International Outreach Programme.
The objective of the programme is to create IBS awareness among developing countries through the platform of international seminars and workshops such as Langkawi International Dialogue and OIC meetings.
Reference:
1. Whitepaper 2003. About Open Building. Bensonwood Homes
2. Third Outline Perspective Plan (OPP3) 2001-2010
3. 2005 Budget Speech, www.pmo.gov.my
4. 2006 Budget Speech, www.pmo.gov.my
5. Economic Stimulus Package Speech, 2003, www.mten.gov.my
Monday, May 28, 2007
IBS Technology Series Certificate Giving Ceremony - 2nd Batch
Serdang, 26 May 2007 - The IBS Technology Series Certificate Giving Ceremony for the 2nd INSEP-IBS trainees was held at the Dewan Taklimat, Engineering Faculty, Universiti Putra Malaysia (UPM) on May 25, 2007 at 11.00 am.
It was a much anticipated event for all the trainees who had attended the programme since January 2007. Two special guests graced this event - Prof. Ir. Abang Abdullah Abang Ali, Director, Housing Research Centre (HRC), and Prof. Madya Ir. Dr. Mohd. Razali Abdul Kadir, Deputy Director, HRC.
The event started with a speech by the Student’s Representative, Mohammad Khairul Anuar M. Noor Kamil. He thanked the lecturers and trainees, saying, “My personal experience with each of you has enriched my understanding of the challenges and issues faced by graduates. Every one of you here inspires me to continue to work with positive mind and attitude.”
Prof. Ir. Abang Abdullah, in his speech, highlighted the current issues of building quality and maintenance in Malaysia and its relation to human capital development programme like INSEP-IBS. He also thanked IBS Modular for working hand in hand with HRC to fulfill the objectives of INSEP in enhancing the employability, adoptability and marketability of the graduates and widen their work scope through re-training in high technology sectors that provides high employment potential.
Prof. Ir. Abang Abdullah and Dr. Mohd. Razali then presented the trainees with a certificate confirming that they had completed the “IBS Technology Series” course. The ceremony ended with a delicious nasi minyak lunch, followed by a group photo session.
During 3-months of “Technology Series”, the trainees have been exposed to wide range of IBS knowledge & design skills. The trainees also gained valuable soft skills and motivational training. For that, IBS Modular would like to thank:
- Professor Madya Ir. Dr. Mohd Saleh b. Jaafar, Professor Madya Datin Dr. Napsiah Ismail, and - Professor Madya Dr. Rosnah Mohd. Yusuff (UPM) for the inputs and guidance
- Illiana Azizan and Siti Hajar (HRC) for the event supports and
- CIDB, Pusat IBS, Setia Precast, Eastern Pretech and He-Con for the informative visits.
Thank you very much – you have made a tremendous impact on the trainees!
INSEP IBS 2007 - 2nd Batch
Friday, May 18, 2007
Modular Coordination in Construction Industry
MS 1064 is a guide line towards the usage of Modular Coordination (MC) in building constructions which consists of Part 1 to Part 10 under the general title, "Guide to Modular Construction in Buildings". It provides the general principles, room and storey heights, coordinating sizes and preferred sizes for various building components, dimensions of elements, components and spaces in the planning and design of building.
Modular Coordination (MC) is a concept for coordinating dimension and space for which buildings and components are dimensionalised and positioned in basic units or modules. MS1064 introduces a certain geometric discipline using practical approaches which relate to set-up coordination and measurement of components and spaces in the building design. The standard specifies that the module basic M = 100mm as the basic unit to be used in a square of M. The introduction of MC in the industry is to improve productivity and quality in building construction construction as well as to act as a tool towards rationalisation and industrialisation of the building industry.
MC has been introduced in Malaysia since 1986, but has not been widely implemented in the building industry. The main factors limiting the uses of MC in building industries is lack of knowledge on MC concept and it requires precision dimensioning and proper planning.
The characteristis of MC are:
- The basic module is small in terms of odd size in order to provide design flexibility, yet large enough to promote simplification in the components' variation in sizes.
- Industry friendly features that not only cater for manufacturing but also the transportation and assembly requirements.
- Ergonomically designed to promote efficiency
- Internationally accepted to support international market
MC Concept
MC may be applied to the design, manufacture and assembly of buildings, its components and installations. It also affects the work positioning and dimensioning during construction. At the work level, MC allows for relative independence in decision making with the common dimensional language. The concept of MC is based on:
- The used of modules (basic modules and multi-modules)
- A reference system to define coordinating spaces and zones for building elements and for the components which form them
- Rules for locating building elements within the reference system
- Rules for sizing building components in order to determine their work size
- Rules for defining preferred sizes for building components and coordinating dimensions for building
The principal objective of implementing MC is to improve productivity through the reduction of wastages in the production, installation process, to improve quality in the construction industry and to encourage an open system. With Open System approach, building components could combine in a variety of individual building projects while ensuring the architect freedom in their designs.
MC is an important factor in application of Industrialised Building System by way of standardization of components ad dimensions such as reduce time of production and installation of components, achieving repeatability and able to construct building at lower cost.
Excerpted from CIDB, IBS Digest Oct-Dec 2005
Friday, March 30, 2007
Kontraktor kelas F disaran serta IBS
SUBANG JAYA: Kerajaan mensasarkan lebih 20 kontraktor Bumiputera terutama kelas F mampu menjadi vendor industri pembinaan negara, khususnya dalam Sistem Binaan Berindustri (IBS) dan pengedar bahan binaan.
Timbalan Menteri Pembangunan Usahawan dan Koperasi, Datuk Khamsiyah Yeop, berkata pembabitan hanya 40 kontraktor Bumiputera seluruh negara dalam sistem berkenaan termasuk sebahagian kecil kontraktor kelas F, pada tempoh tiga tahun, menunjukkan perkembangan agak perlahan.
Jumlah itu, katanya, adalah terlalu kecil berbanding bilangan kontraktor berdaftar dengan Pusat Khidmat Kontraktor (PKK) sehingga bulan lalu, seramai 46,473 kontraktor dan 32,022 daripadanya adalah kontraktor kelas F.
Beliau berkata, jumlah itu juga membabitkan kontraktor yang mengeluarkan produk binaan secara kecil-kecilan.
Sehubungan itu, katanya, kesedaran supaya kontraktor terutama kelas F memperluaskan cabang kerja masing-masing perlu dipertingkatkan, bagi memastikan mereka tidak berharap terhadap kerja pembinaan semata-mata.
“Kontraktor perlu didedahkan dengan meluas faedah menyertai IBS yang menggunakan teknologi berbeza, berbanding cara konvensional digunakan sebelum ini,” katanya pada sidang media, di sini, semalam.
Tuesday, March 27, 2007
Why Knowledge Management Crucial for the Realization of National IBS Roadmap
Authors :Nik Ahmad Faizul, Industry Development Director, Innovacia Sdn Bhd & Wan Amrul Wan Mustafa, Chief Knowledge Architect, Innovacia Sdn Bhd
Knowledge was the driving force behind the Industrial Age. It was somehow subsided and nearly forgotten until the next wave arrived which is the Digital Age. This new age has re-surfaced knowledge again as one of the key dimension to propel global growth. Hence, Knowledge Management (KM) is now an important discipline and an essential source that our economy cannot afford to do without, if we are to have competitive advantage and remain relevant.
In Wikipedia, KM refers to a range of practices used by organizations to identify, create, represent, and distribute knowledge for reuse, awareness and learning across the organization.From business standpoint, Harvard Business Review refers KM as the way companies generate, communicate, and leverage their intellectual assets.
We have also seen over the last ten years, highly significant event took placed on the advancement and explosion of information and communication technology (ICT) driven by the liberalization of global economies. This has lead to tremendous transformation in the manner businesses are being executed. The world is not only becoming borderless but also flatter instead of round as the bestseller writer, Thomas L Friedman put it. Information are now highly accessible and being exploited to an unimaginable scale. The rat race for market positioning is as fierce as ever through the capitalization of information, knowledge and innovation.
This scenario has also lead major economies to have greater access than ever before into countries such as India and China to exploit its competitive resources leading to a more competitive product and services in the marketplace.
With this challenging phenomenon, it is now overdue and absolutely critical that we need to expedite our readiness, the know-how and competitiveness of our Malaysian Construction Industry in order to survive and sustain; an industry which is now minus 1.6% growth based on year 2005 government statistic. The fragmented nature of our industry need to be consolidated and reconstructed in order to realize the government’s aspirations on the National IBS Roadmap which targets the industry to be industrialized by the year 2010.
As part of efforts to steer various sectors towards our Vision 2020, the Malaysian government has also launched the National Knowledge-Based Economy Masterplan which was first announced by the government in the Budget 2000. This masterplan marks yet another key government initiative to further accelerate the development of the nation into a knowledge-based economy. It provides strategic framework outlining the changes to the fundamentals of the economy.
These National IBS Roadmap and Knowledge-Based Economy Masterplan have provided a good base information related the policy targets and objectives. However, this information alone will not progress our industrialisation effort. It is only a reference document on policy direction. As such, strategies still need to be formulated downstream within each sector. In doing so, we need to capture our industry knowledge, consolidate, reconfigure and strategise to our best competitive advantage, in order to progress.
To one of KM guru, the late Peter Drucker, leaders often mistake information for knowledge. Information is data endowed with relevance and purpose. Converting data into information thus required knowledge. And knowledge, by definition, is specialized.
Another misconception on KM is that it is ICT oriented. ICT is purely a tool to an end. It should not be treated as the driving factor for KM. Business strategies and direction instead, are the true drivers for KM.
With a cohesive and collaborative effort involving government and industry, we are in position to consolidate our fragmented industry information and ignite our latent intellectual assets. We believe such assets do exist based on our exposure in national mega infrastructural projects over the past 15 years as well as the world is now being flatten with information at the press of a button.
“A company(as an industry member) is not a machine but a living organism”.- Ikujiro Nonaka, KM Guru specialising on Japanese Business Strategies. However, efforts on the ‘HOW TO’ for the National IBS Roadmap seems way behind and need to be urgently accelerated. One of the key factor for this delay is that the industry by nature, is very much project based instead of program based. The soft aspect has not been fully exploited especially on the management of industry knowledge.
A knowledge based construction industry would induce a conducive environment to propel the acceleration of our IBS Roadmap. However, current mindset on ‘information protectionism’ need to be phased out. This is very much due to the current ‘Red Ocean’ overcrowded marketplace whereby companies are engaged in head-to-head competition struggling to survive, let alone to sustain.
IBS on the other hand, is a new industry with endless opportunities. In order to commence with this exploration, it has to start with knowledge sharing as the new working culture within the industry. This approach encourages investment on ‘trust’ which in turn, will lead companies who used to be in competition, to better understand each other and collaborate for improved market positioning in this new ‘Blue Ocean’ industry.
It is only with this ‘Open Collaboration’ environment that we are able to induce participation, develop and steer, impactful downstream strategies to support the roadmap implementation.
This effort on KM however, need to be driven from both top and bottom ends of industry heirarchy. Apart from being policy driven, each industry organization plays an equally crucial role in developing industry’s intellectual capability. This effort will result in the organization to be more specialize and therefore provides an improved strategic positioning for the industry as a whole.
“ To remain competitive – maybe even to survive, businesses will have to convert themselves into organizations of knowledgeable specialists.” - Peter Drucker
Based on the above, we need to create our own speciality and niche in order to sustain. It is only through KM that this can be achieved and therefore, necessitates companies to review their internal organizational strategies and methodologies.
The essence of KM in an organization is best put forward by Alex Bennet, former Chief Knowledge Officer of US Department of Navy. She describes the essence of knowledge management is built on intellectual capital, which includes human capital, social capital and corporate capital. All three are essential components of enterprise knowledge (see diagram).
Human capital is our greatest resource. It is made up of an individual’s past, present and future. Social capital related to communications, human and virtual networks, relationship, collaborations, etc. As for Corporate Capital, it covers intellectual property, corporate assets and organizational processes. Knowledge Management can be viewed as a process for optimizing the effective application of intellectual capital to achieve organizational objectives.
The current industry however, perceived as having assets, financial capital and staff would be sufficient to realize company objectives. It is more focus on the tangible aspect of the organization. The crucial intangible elements were completely overlooked and this has impacted our competitiveness.
In conclusion and as way forward, we clearly need to diagnose ourselves as individual, company, associations, industry as well as the policy makers on how far are we in our positioning to persevere the demanding and exhaustive rat race for market positioning, and most critically our existence and sustainability in the current Globalization era.
The ultimate way forward is for us to inject into ourselves intellectual knowledge which will lead us to the Know-How by becoming the specialist within the marketplace. This can be achieved by being more open minded, unbiased, neutral, patriotic, emotional and aggressive in our efforts to support and participate in the realization of the National IBS Agenda.
Tuesday, March 20, 2007
Better Houses for All
The Star, Saturday April 22, 2006
SHAH ALAM: Prime Minister Datuk Seri Abdullah Ahmad Badawi wants good quality and affordable homes set in comfortable neighbourhoods for the people. The houses must also be the result of responsible development, he said at the launch of the Housing and Local Government’s computerised “open registration system” for low-cost houses at the state secretariat building here.
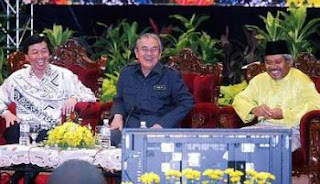
Abdullah also wanted a comprehensive ICT database set up to help house buyers obtain necessary information like the location of housing projects and pricing, among other things.
“Some people (want to) buy homes in places far from where they are living, some near their kampungs to settle down in after retirement,” he said. “So, it is good to have a database on homes giving details like where they are to be built, pricing, and whether they are located near towns.”
Abdullah said housing developers must be responsible and look into various factors like environmental implications before launching projects. “One cannot foresee what can happen in housing areas. Places which had never been flooded before have become flood prone after houses are built there,” he noted. He said irresponsible developers often took the easy way out like cutting down trees and dumping soil into rivers for their housing projects, which in the end caused flooding.
Monday, March 12, 2007
The House of the Future
Article excerpted from Popular Science Magazine, November 2006
Imagine if cars were built the way most houses are. A procession of trucks would deliver materials and parts to your driveway – sheet metal, spools of wire, screws, pistons, a roll of carpet, bumpers and a steering wheel. Then day laborers would arrive to put it all together. In the rain. It sounds absurdly efficient, yet that’s the accepted way of constructing a modern American house.
While cars, computers and other products have improved dramatically in recent decades, houses have changed almost as little as the methods used to build them. “Every product except homes has become more sophisticated, with higher quality at lower cost,” says architect Kent Larson of the Massachusetts Institute of Technology."Homes are just the opposite.”
Larson is perhaps the country’s lead proponent of a radical new approach to designing and constructing homes. The house of the future, he says, should be more like a personal computer or a car. It should be affordable, built mostly in a factory, and with parts that are easy to repair or replace. You should be able to design your own home online, just as you can today with a Dell laptop or a Honda minivan. The key to making it happen? Follow the lead of other industries: standardize and accessorize.
Take personal computers. Products made by competing manufacturers are standardized for compatibility. You can buy virtually any printer or mouse on the market, and it will work with the computer you already own. “Nobody has to agree on what a mouse is; you just have to agree on the USB port,” Larson says.
Before houses can be built this way, though, the industry needs standards analogous to the USB standard for computers. “You don’t have to agree on the toilet, but you have to agree on how the toilet connects to the wall or the floor,” Larson explains. That may sound easy enough, but getting dozens of manufacturers to sync their johns will require fundamental changes in the homebuilding industry.
A House Made to Order
Prefabricated components – like walls, floors and plumbing – make home construction a snap
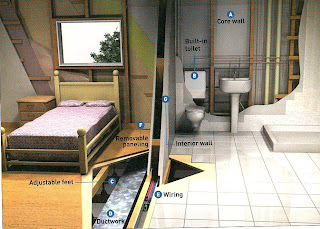
One of the key components of the MIT Open Source house is the core wall [A], a prefab unit into which all of the plumbing is already installed. Even the toilet [B] is built directly into the wall instead of attached to a waste drain on the floor. The core wall is simply hooked up to the service lines, and then the tiling and fixtures (sink, shower) are added to complete the bathroom. The house’s flooring is fitted with adjustable feet [C], which rest on the subfloor and provide soundproofing and space for HVAC ductwork [D]. The electrical wiring [E] is easily accessible behind removable paneling [F], making installation of extra outlets easy. Finally, the interior walls [G], which also arrive fully assembled, are snapped into place to form rooms.
Wednesday, February 28, 2007
Syor sistem kontrak berpusat elak ketirisan
Rabu, 28 Februari 2007
KUALA LUMPUR: Kementerian Kewangan diminta mewujudkan sistem perolehan kontrak berpusat bagi menyokong penyertaan Bumiputera mengeluar dan membekal komponen Sistem Binaan Berindustri (IBS) dan mengatasi masalah ketirisan.
Menteri Pembangunan Usahawan dan Koperasi, Datuk Seri Mohamed Khaled Nordin, berkata Mara kini giat membangunkan usahawan Bumiputera dalam IBS serta rangkaian peruncitan bahan binaan oleh golongan itu, sejajar galakan kerajaan menggunakan pendekatan IBS bagi projeknya.Katanya, IBS iaitu bahan binaan yang dihasilkan di kilang sebelum dipasang di tapak, tidak memadai menggalakkan Bumiputera menceburinya termasuk membuka kilang mengeluarkan komponennya, jika terhad bagi projek di bawah Mara saja.
Langkah akhir menentukan IBS menjadi amalan di negara kita dan penyertaan Bumiputera secara berkesan ialah kerajaan dapat melahirkan satu sistem yang mana perolehan bagi komponen dikeluarkan Bumiputera ini dilaksanakan melalui satu perolehan berpusat atau central contract.“Atas sebab itu kementerian akan memberi pandangan kepada Kementerian Kewangan supaya disyaratkan kontrak berpusat komponen IBS.itu baru ada jaminan terhadap komponen dikeluarkan,” katanya.Beliau berkata demikian selepas merasmikan Forum Peluang-Peluang Perniagaan Bumiputera Melalui IBS dan Peruncitan Perkakasan Industri Pembinaan di Pusat Dagangan Dunia Putra di sini, semalam.
Aplikasi IBS selaras saranan Perdana Menteri, Datuk Seri Abdullah Ahmad Badawi yang mahu mengurangkan jumlah tenaga kerja asing di Malaysia yang mencecah 250,000 orang. Ia juga menyingkatkan tempoh penyiapan projek serta meningkatkan aspek keselamatan dan kebersihan tapak.Masalah ketirisan projek Bumiputera sebelum ini turut dikaitkan kurangnya penyertaan golongan itu dalam perbekalan bahan binaan, mewakili 60 peratus kos projek.Mohamed Khaled berkata, pihaknya mahu syarikat Bumiputera mengeluarkan antara 100 hingga 120 komponen binaan daripada 400 komponen yang ada dalam industri itu.Katanya, kementerian mahu memastikan Bumiputera melengkapi rantaian nilai industri termasuk menjadi pemasang bahan binaan itu serta perunding.
Kita sudah lantik 15 syarikat Bumiputera membabitkan projek UEM di Putrajaya,” katanya.Mohamed Khaled berkata, program membangunkan rangkaian perkakasan dan bahan binaan pula termasuk menyediakan 14 mentor iaitu satu pada setiap negeri dan 56 mentee, sebagai pembekal utama dan sampingan membekalkan bahan binaan Bumiputera.
Tuesday, January 30, 2007
High Performance Building Characteristics
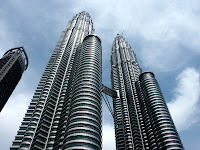
Monday, January 29, 2007
Modular construction: Pros and Cons for lab building
A combination of factors—such as unprecedented construction cost escalation, demand for instant research space driven by shortened funding cycles, and challenges in finding qualified construction labor—are forcing design professionals and their clients to look for new ways of designing and constructing laboratories. Facilities professionals are considering alternatives to the traditional approach to construction projects, and this has led to a rise in the use of modular techniques for research laboratories.
Modular design, of course, is standard practice for most of today’s research building projects and for many other types of lab buildings as well. Modular design is characterized by regular repetition of structural elements and mechanical and utility infrastructure within the floorplate of a traditional “stick-built” facility: one constructed on site from the ground (or underground) up. Modular construction, however, means literally creating a building from discrete modules fabricated off-site.
During the past 10 years, the pharmaceutical industry has used modular construction to provide production facilities to meet tight manufacturing schedules and extremely rigorous FDA requirements. Today, that schedule and quality pressure is moving up the drug discovery timeline into the research sector. The time allocated to design, bid, and build some laboratory projects is now just too short to accommodate traditional methods. In addition, the quality of construction labor available in some locations is simply not appropriate for today’s complex laboratory environments. Project teams and clients must consider multiple factors when investigating modular lab construction. An owner must be well aware of these issues should be careful when approaching the “stick-built vs. modular” decision.
Modular construction: An overview Modular laboratories are constructed from compartments to form a cohesive building. A laboratory is manufactured in modules in a production facility, assembled for pre-testing, disassembled for shipping, then transported to the construction site and reassembled.
Modular science buildings have been used for more than 20 years, historically for pharmaceutical manufacturing facilities as well as the ubiquitous “trailers” found on most research campuses that provide temporary and swing space. With today’s demands, however, modular lab producers are teaming with design firms to develop full-blown laboratory facilities delivered in a shorter time and with attractive solutions that go beyond the standard “shipping container” aesthetic.
Working with the owner, a team of experienced architects, engineers, and other design professionals first develop a schematic design for a proposed laboratory that considers the opportunities and challenges of modular construction and compares it carefully to conventional construction. Only after the schematic design is fully developed does the owner enter into a contract agreement for a modular lab building. This agreement would be similar to a design/build arrangement; an owner would contract with a manufacturer to complete the design, then manufacture and construct the building.
Working with the owner and the design review team, the manufacturer takes responsibility for design, construction methods, and costs. The manufacturer then designs the facility, in many cases with the help of an architect specializing in laboratory design. The manufacturer then constructs the modules inside a factory in a controlled environment.
One big advantage of modular construction is that the construction schedule is not subject to the seasons and weather patterns. In addition, factory construction allows for parallel paths for different systems and simultaneous work on separate modules in different stages of completion. There is access to the work from all directions, and there is standardization of repeated activities. The manufacturer is able to reuse designs for standard building blocks so that there is less fundamental engineering. These factors result in a significantly compressed construction schedule. Owners have reported time savings of six to 12 months from a traditional fast-track project.
Modular construction: Pros and cons
Pros:• Can cut six to 12 months off the project schedule.• Reduces cost escalation compared with a traditional project by virtue of speed. • Allows for construction of complex, high-quality projects in areas where there is a shortage of skilled tradespeople.• Increases quality of final product due to factory-style quality control.• Minimizes site disruption due to reduced need for on-site staff, lay-down areas, and machinery. • Increases safety due to less on-site effort.
Cons:•Costs can be greater than stick-built, depending on transport costs. These costs may be mitigated by lower labor costs in some local markets.• Changes in the design after manufacturing begins can be difficult and expensive to accommodate.• Clients may worry that exterior systems may not deliver the desired image.• Height and area limitations exist due to construction type.• The code compliance and inspection process will likely be more complex than with a stick-built facility.• Future flexibility and adaptability may be reduced to a degree.• The potential exists for creating a labor dispute with local unions.
Greg Muth is an associate and laboratory planner with Flad & Associates in San Francisco. Flad & Associates (www.flad.com) is a national planning and design firm with 250 staff serving the science and technology, healthcare, and higher education markets from five offices throughout the U.S.
Sunday, January 21, 2007
INSEP - 2nd Intake for IBS trainee
> for graduates who seek fresh knowledge in IBS <
NOW OPEN!
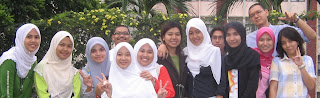
Book your place as soon as possible as this will be on a first come first serve basis. Only limited placement available. Please contact:
Pn. Maniza Ismail o3-8315 7843
It's FREE! Fixed monthly allowance of RM500! Up-to-date industry knowledge & work experiences & much more!
INSEP is conducted by Advanced Manufacturing Institute (AMI) Shah Alam; an institution dedicated in providing quality training and education programs. In collaboration with industry, education and professional institutions, we invite YOU to join our programme in Industrialised Building System (IBS)
What does INSEP offer?
Participants will undergo intensive skills development programme conducted by highly capable trainers. It is aimed to increase the employability and marketability of participants. The programmes are as follows:-
1. Personal Development Series (2 months)
a. Communication English
b. Presentation & Negotiation Skills
d. Experiential Learning
e. Project Management
f. Problem Solving & Decision Making
2. Technology Series (3 months)
a. Introduction to Construction/IBS Industry
b. Construction & Materials Technologies
c. Green Card Course
d. Design & Analysis
e. Modular Coordination (MC) & MS1064
f. IBS Content Scoring System
g. Manufacturing Process and Management
h. Site visits
3. Industrial Attachment (7 months)
Attachment at IBS company throughout Malaysia
Am I qualified?
If you meet these 3 requirements, you're exactly the person we're looking for.
1. Malaysian graduates from 2oo3 onwards from public or private higher learning institutions either local or overseas.
2. No previous employment history related to the degree/diploma. Part-time job history is acceptable.
3. Degree or Diploma graduates in
a. Civil Engineering
b. Architecture
c. Building Engineering
d. Mechanical Engineering
e. Electrical Engineering
f. Quantity Survey
g. Design / Production Engineering
h. Other related field
Is it recognised?
Yes, INSEP certification will be awarded by the Advanced Manufacturing Institute (AMI) and technology partners.
Inquiries
For further details on INSEP, IBS or interview attendance confirmation, please contact :-
Pn. Maniza Ismail Tel : o3-8315 7843 Fax : o3 8888 8232 e-mail : maniza@might.org.my
Saturday, January 20, 2007
MiGHT's initiatives in Construction and Housing
The industry itself is as old as the country but there has been little in the way of development, particularly in terms of technological innovation. To further compound the problem, the construction industry is heavily dependent on foreign labour. Recognising the need for improvement, Malaysian Industry-Government Group for High Technology (MIGHT) formed its MIG in Construction and Housing in 1994. It was determined that there were various key issues that needed to be addressed.
Among the issues highlighted are the prolonged dependence on foreign labour has led to the industry continuing to use labour intensive production techniques. In its attempts to introduce innovation to the construction industry as well as overcoming the labour dependence and shortage, MIGHT has determined that the way to move forward is to keep abreast with new technology in order to be more competitive. The implementation of a new method of construction, which was based on a modular concept, would result in a greater output of more affordable housing units.
Industrialised Building Systems (IBS) is a method which enables a company to move away from the conventional labour intensive method of construction to a more technological based. With this approach, components of the building are manufactured off-site, in modules so to speak, and brought on site to be assembled. The standardisation of elements and fittings of houses will ultimately lead to an increase in efficiency, better quality and less wastage of time and materials. Most importantly it will provide for a lower cost structure. The cost structure is important here as affordable housing can be built to support the governments low-income housing schemes.
The industrialised modular concept also allows for the manufacture of large or small units as the components are interchangeable and easily assembled. The pre-fabricated composite materials can also be used to further develop the industry by catering to the export market.
At present there are pockets and elements in the industry that could become the basic ingredients for the industrialisation process through the IBS concept. With over fourty years of laissez faire implementation in Malaysia, IBS has not become widely accepted or used. Experiences in countries like Singapore, Denmark, Norway etc. indicates a strong government intervention is needed for change in the construction industry and a successful implementation of IBS. The MIG in Construction & Housing is committed to ensure the success of IBS implementation that will form the impetus for the migration of the traditional insitu industry to one where the supply of components will form the basis of construction delivery.
Thursday, January 18, 2007
Industrialised Building Systems - An Overview
“The Industrialised Building Systems (IBS) promises elevated levels of expertise throughout the industry, from manufacturers, installers, engineers, planners, designers, and developers. The benefits of IBS are numerous and far reaching. Reduced construction time, better site management, reduced wastage are but a few of these benefits, that will ultimately produce better products for the population.”
YBhg. Dato’ Seri S. Samy Vellu
Minister of Works, Malaysia
Industrialised Building System is an alternative approach of construction that will definitely change the scenario of the current local construction industry towards a systematically approach of mass production of construction materials. Prefabricated components of buildings which are conceived, planned, fabricated from factories will be transported and erected on site. With this method, the process would involve planning; management and sustained improvement of the production process to eliminate waste and ensure the right components are produced and delivered at the right time, in the right order and without defect. In this respect, the construction industry has a great deal to learn from the manufacturing sectors that have long been emphasizing on quality and minimising defects. IBS will definitely among others reduce unskilled workers in the country, less wastage, less volume of building materials, increased site cleanliness and better quality control.
In the Malaysian context, five common types of fully developed IBS have been identified as shown.
1) Pre-cast Concrete Framing, Panel and Box systems
IBS Projects in Malaysia
IBS is not new in Malaysia and have been around since the early sixties. The first pilot project was initiated by the Government and it was along Jalan Pekeliling which involved 3,000 units of low cost flats and 40 shop lots. However, developments in IBS after that failed to gain support from the industry and consumers. From a survey done by CIDB on 2003, it was found that the percentage usage of IBS in the local construction industry is only at a mere 15%. However, several major world class developers in Malaysia have used some percentage of IBS in their projects. Several projects that use IBS can be seen as follows.
i) KLIA
ii) Government Quarters in Putrajaya
iii) Petronas Twin Towers
iv) KL Sentral
Among the reasons that have made IBS not very popular with the developers would be the abundance of cheap foreign labours in the country. Currently there are about 250,000 workers in the construction industry. The Government’s effort to reduce the foreign workers to not more than 15 percent of the country’s labour force in the next five years would be an impetus for the local developers to use IBS. By using a superior construction technology that requires highly skilled workers, the dependence on foreign workers would significantly be reduced.
IBS Roadmap 2003 – 2010
On October 2003, an IBS Roadmap 2003 – 2010 has been tabled by the Ministry of Works to the Cabinet and subsequently has been endorsed by the Cabinet to be the blueprint document for the industrialisation of the Malaysian construction sector. The blueprint that have been produced by the IBS steering committee and working groups, organized by CIDB will be a reference point for all parties to implement all the programmes towards industrializing the Malaysian construction sector. The programme’s that will be implemented is hoped to meet the objective of total industrialization of Malaysia’s construction sector by 2010.
Under this roadmap, MIGHT through the Office of the Science Advisor have been tasked to develop an IBS vendor programme for the nation together with the Ministry of Finance and Ministry of Entrepreneur and Co-operative Development. The IBS vendor development programme will consist of existing and new industry players and covering a wide spectrum of activities, from preliminary design to the assembly and installation of housing projects. Towards this end, MIGHT is constantly in consultation with other stakeholders such as the Ministry of Housing and Local Government, Construction Industry Development Board, Ministry of Entrepreneur and Co-operative Development, SIRIM and other related agencies to develop a comprehensive vendor development programme.
Several ingredients will need to be in place for the development of the vendor programme. Among them are identifying the vetting agencies that will provide a control uniformity of design and quality of the components produced by the vendor. The vetting agencies will also maintain standards and ease the legislative problems. The investment requirements for setting up a factory to manufacture components by the vendor are estimated to be about RM1.25 million (excluding land) and dependable on the type of components to be produced. This level of investment is within the reach of small and medium contractors.
With Budget 2005 announced recently, the Government is committed in ensuring IBS implementation by providing an additional of 100,000 units of affordable homes to be implemented using IBS. Budget 2005 also reveals Government intention in increasing the IBS usage in Government building projects from 30 percent currently to 50 percent starting from 2005.
On achieving a wider scale implementation of IBS scale for Malaysia, the Government will also give full exemption on levy imposed by CIDB for developers who utilize IBS components exceeding 50 percent. These wise decisions made by the Government will definitely create a lot of interest from the industry to use IBS as an alternative approach of construction. The next stage of IBS would be to explore the ‘export’ of the system to overseas market. The success of these efforts will enable the local construction industry to be competitive and penetrate the global market.
Reference:
Industrialised Building Systems (IBS) Roadmap 2003 – 2010. 2003. Construction Industry Development Board.
Waleed A.M. Thanoon, Lee Wah Peng, Mohd Razali Abdul Kadir, Mohd Saleh Jaafar and Mohd Sapuan Salit. September 2003. The Experience of Malaysia and other countries in Industrialised Building System Universiti Putra Malaysia
Foreign Labour to be limited to 15 percent. 12 September 2004. New Straits Times Press
Budget 2005. 10 September 2004. Ministry of Finance